How To Eliminate Picking Problems At The Warehouse?
Eliminating picking problems at the warehouse: What can be done to minimize errors?
E-commerce is now becoming one of the fastest-growing sectors of the global economy. In fact, it is predicted that it will grow into a staggering $4.9 trillion market within a couple of years at most.
This is an almost exponential increase in retail transactions, which is why it is imperative for companies to hire highly skilled workers for picking, receiving, packing, and loading products, in order to keep pace with the ever-rising tide of orders.
The issue is that skilled and experienced labor is becoming increasingly hard to find and even more difficult to retain in a large number of markets all around the world. This has taken a toll on productivity and the quality of the work. Picking problems invariably lead to refunds and returns and upset the whole working cycle.
However, there are certain ways through which such problems can be resolved or minimized, at the very least. Let us take a look at a few of these promising solutions:
o Location Finding Technologies
These technologies leverage RFID tags in order to transmit asset-related data both to and from mobile handheld devices carried by pickers and sorters at the warehouse. There are many real-time locationing solutions that are ideal for all budgets and warehouse sizes. They can help to significantly reduce search time and also provide automated and error-proof inbound and outbound deliveries.
o Using ‘Pick IDs’
Each picker should have their very own “Pick ID.” This way, it will be possible to safely monitor every picker and check which ones are making the most mistakes. The ones that deliver 100% of the time will be given awards and bonuses, thus increasing higher quality output throughout the department.
o The Elimination of Paper
Eliminating paper-based documentation from the warehouse has many advantages. It aids in the removal of the ‘human error’ element. Apart from that, increasing the usage of warehouse management software with the help of mobile apps can also significantly streamline service and decrease picking problems. This way, it is easier to ensure that every order is shipped on time, and with a high degree of accuracy so that there is no chance of a return/refund.
Conclusion
The above methods can be uniformly applied to just about any warehouse to ensure that delivery procedures are streamlined and the chances of wrong or delayed shipments are minimized to as great an extent, as possible.
Talk to one of our Printer & Barcode Specialists to learn how to improve your warehouse picking now call (800) 643-2664 .
Reference Links:
o https://www.newcastlesys.com/blog/bid/349401/picking-error-problems-suggestions-and-solutions
Related Links:
https://www.midcomservicegroup.com/barcode-scanner-repair
https://www.midcomservicegroup.com/refurbished-barcode-scanners
https://www.midcomservicegroup.com/barcode-scanners-mobile-computers
https://www.midcomservicegroup.com/are-unreadable-barcodes-causing-you-grief-and-compliance-fines
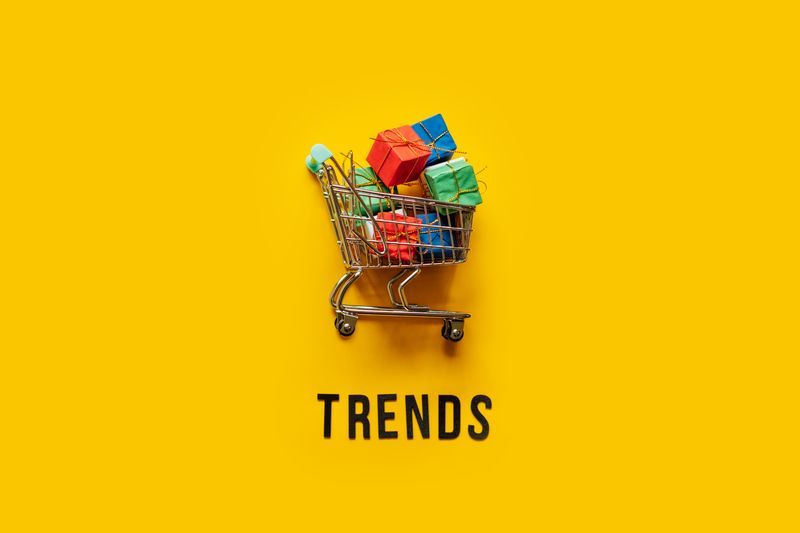