What To Know About Traceability In Manufacturing
What should manufacturing companies know about traceability?
Motorola has written a handy quick reference guide* which outlines all the ‘must-knows’ in the traceability for all those involved in manufacturing. Found it interesting and thought it might be food for thought, so I took it upon myself to sum up the main aspects.
Let’s take a moment to step back and refresh our memories on what exactly traceability is. ISO 8402 defines it as “the ability to trace the history, application or location of an entity by means of recorded identifications”*. Sounds pretty simple, right? Well, factor in the complexities of globalization, increased competitive markets, additional government regulations, safety and environmental concerns it can get a little complicated. As these demands and factors increase, so does the need for timely traceability by manufacturers. Manufacturers must be able to timely track and trace each component of their products from pre-production all the way through to delivery, and after.
Key Reasons for Traceability:
- High Direct and Indirect Costs of Recalls: The fines for non-compliance are extremely expensive. Not only are the direct costs associated with removing the product from market, replacement costs, legal costs, testing and inspection fees, but so are the indirect costs (higher future costs of insurance, testing, regulatory, staffing requirements).
- Increased Compliance Mandates: A few examples include: NHTSA TREAD Act of 2000; US Dept. of Defense requirements, Aerospace Spec 2000 and SEMI standards; The Food Safety Enhancement Act; the Food Safety & Tracking Improvement Act. Traceability can ease the burden and lessen the chances for fines and penalties associated with noncompliance and meet the challenges of stricter government regulations by providing detailed product histories to meet standards and regulations.
- Minimization and Management of Product Recalls: Proactive attempts to minimize negative impact and damage control to brand image, reputation, and customer loyalty. Recalls can be widespread and global in nature.
Examples of Traceability Solutions:
- Serialized container and individual part tracking
- Built-in bar code printing and scanning
- RFID
- Direct part marking
Traceability Solutions can be broken down into 5 key components:
1. MES (Manufacturing Execution System)
- Provides detailed historical information related to production, inspection, genealogy and usage
- Captures component lot/serial numbers per finished assembly
- Documents variables (temperature/pressure) at the time of manufacture
- Identifies a specific person on a specific production shift
- Creates a template for the manufacturing system to guide all steps in production
- Tracks work in process (WIP) and provides insight into production of all current orders and the status at each stage of production
2. ERP (Enterprise Response Planning System)
- MES layer integrates with the ERP system
- ERP has the master information on materials, suppliers and vendors, while the MES tracks the production shop orders including component consumption, WIP and finished goods
3. Data Capture & Mobility Hardware
- Mobile computers, bar code scanners, RFID tags and readers, and industrial WLAN work in sync to capture build information. This allows the MES and ERP system data to be available to mobile workers in real time.
- Devices to capture all traceability methods (ie. 1D and 2D bar codes; RFID; direct part marking; laser etch; dot peen; chemical edge; stamped)
4. Additional Software Systems
- Applications that create mobile and fixed reader front-end interfaces to MES and ERP systems, quality and lab systems, allowing users to access key enterprise applications on mobile devices or allow for automated data capture via fixed readers.
- Management software to manage, maintain and monitor mobile devices; and manage, monitor, and ensure security and compliance within wireless networks.
5. Professional Services
- Designs and implements traceability solutions within manufacturing environments through consulting, project management and vendor selection
These traceability solutions can provide many benefits to manufacturers throughout the supply chain stay on top of the game and effectively manage and track all their entities. Other than the key reasons for traceability as stated above there are additional benefits for implementing traceability solutions into your process:
- Increase customer satisfaction and safety, thus reducing costly expenses and customer impact
- In the event a recall does take place, manufacturers are able to minimize the impact by only recalling those items with the specific serial numbers that were built with the faulty component, material or process – thus significantly reducing expenses and customer impact.
- Improve data accuracy
- Increase operational productivity
- Mobile track-and-trace solutions can prevent quality issues before they occur or, in the event of a product recall, allow manufacturers to act swiftly as well as narrow the scope of the recall to reduce exposure to negative brand impressions and damage to revenues.
- Reduce warranty claim costs, and contribute to improved product quality in the future.
For further information on the various traceability solutions mentioned and for all your bar code labeling and printing needs, call us as (800) 643-2664 and immediately talk to one of our friendly representatives; or chat us up on Facebook , Twitter , Google+ and LinkedIn !
Keep your thermal label RFID printers running! Download our FREE eBook now.
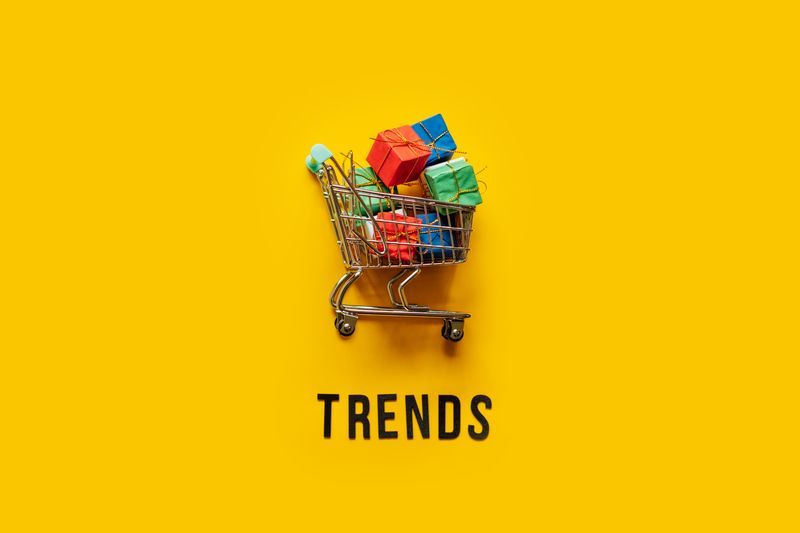